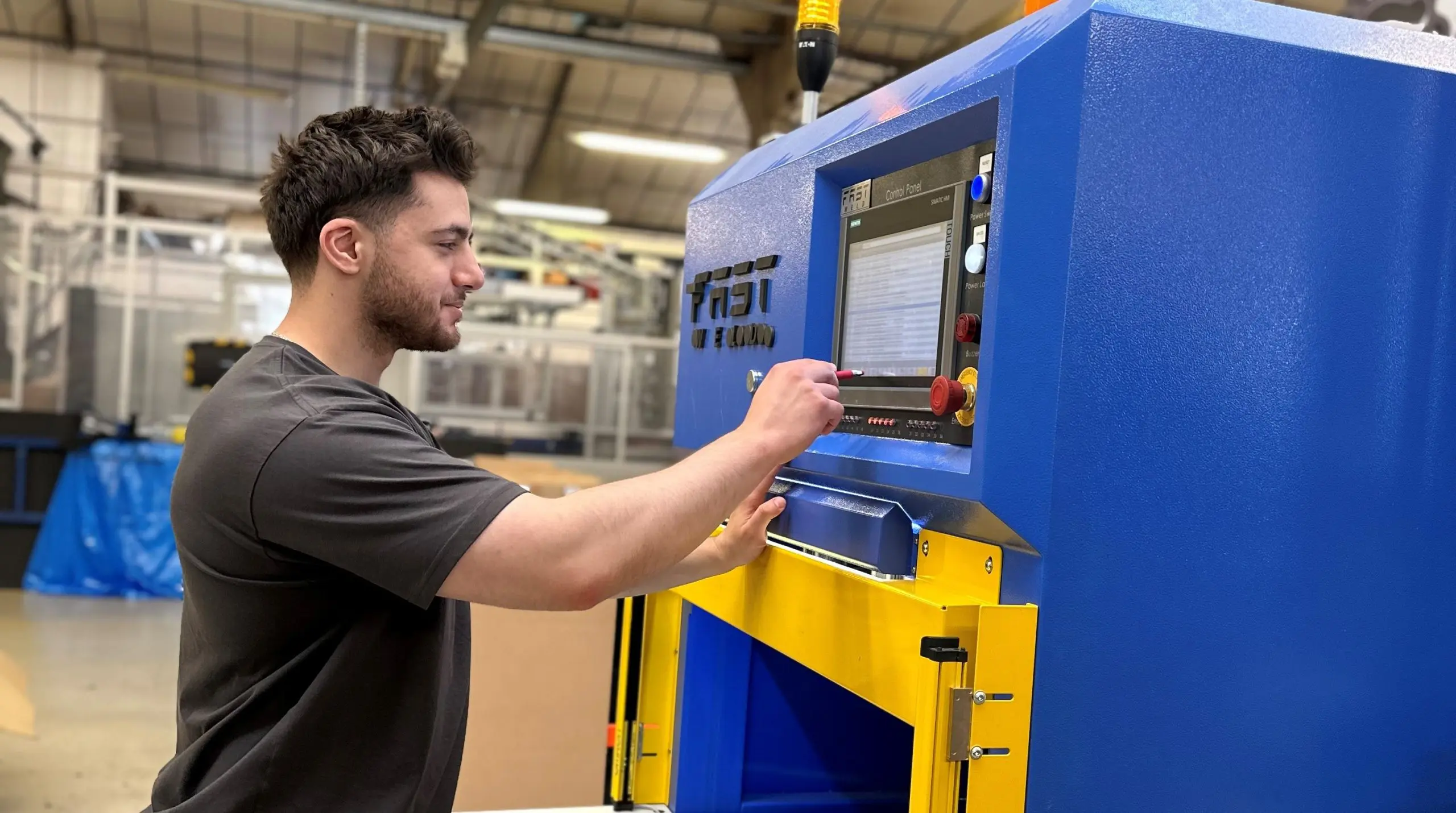
12th June 2025
Production Operator, CNC Team
Read more >
At Kewell Converters, we’re proud to support and develop talented engineers who are shaping the future of foam fabrication. Our team thrives on a combination of experience and fresh perspectives, blending tried-and-tested techniques with innovative approaches. Today, we’re introducing Joel, an upcoming star in our engineering team who has recently been promoted to CAD/CAM engineer. His journey at Kewell Converters shows the exciting opportunities in foam conversion.
Joel’s career path has been anything but traditional. Before joining Kewell Converters two years ago, he worked in IT as a cloud engineer for Fidelity, spending long hours working remotely during the COVID-19 pandemic. Prior to that, he had aspirations of becoming an architect and worked as a consultant for Salesforce. His passion for STEM subjects led him to study applied science and IT, making his transition into engineering a natural progression.
When Joel joined Kewell Converters, he started as a Production Operator, working late shifts. But his drive and curiosity soon saw him moving up the ranks. Six months ago, he transitioned into the office as a trainee design engineer, and shortly after, he was promoted to CAD/CAM engineer a significant new role that Kewell Converters have created.
Joel’s work revolves around programming the machines that create precision foam parts. His job has two main components: writing the programmes that dictate how our machines operate and then fine-tuning the code to ensure efficiency. This requires an in-depth understanding of how our three CNC routers function, as each machine has different parameters and requires unique programming.
For most foam parts, Kewell Converters develops custom programmes that dictate the cutting and shaping process. Some projects are straightforward, like a basic foam insert for a case, while others require extensive programming. For example, a recent project for the retail industry took over a week of programming alone—an exceptional case but a testament to the complexity of foam engineering.
One of the projects that Joel has witnessed at Kewell Converters and been most curious about the engineering involved is the fabrication of a huge shield-shaped foam dome as well creating housing for a defibrillator to sit inside a box that would be kept up on a mountain and needed to withstand extreme -40°C conditions. This was the eighth version of the part, showing the patience and precision required in foam fabrication. Another key area that Joel has enjoying learning about and have involved pushing the boundaries of foam design and engineering is producing MGR panels—these are specialised foam parts used in aircraft interiors. These panels must meet strict aerospace regulations, and Kewell Converters has been experimenting with different speeds and feeds in the programming process to improve efficiency. Some of these parts take up to 12 hours to cut, highlighting the level of precision and expertise needed in foam conversion.
Despite the technical challenges, Joel loves to continually push the boundaries of what’s possible in foam conversion with every project and every day so, so different . He acknowledges that some things are simply not feasible due to material limitations, but that doesn’t stop Joel from exploring new methods. Manual tool changes remain a challenge, as they introduce downtime, but Joel and the team at Kewell Converters are always looking for ways to optimise production.
Joel is particularly excited about the potential of artificial intelligence in foam fabrication. He has been researching AI applications in programming and manufacturing and is very open to learning about new more efficient ways to produce parts and tackle projects aiming to integrate smarter systems into our workflow. He’s also been involved on a new R&D project which could revolutionise foam production and could introduce a whole new approach to foam conversion.
Joel’s typical day starts early, prioritising programmes that need adjustments before production begins. Once this work has been done, he shifts to developing new programmes or refining existing ones, collaborating closely with the wider operations team to understand their processes and ensure seamless execution. On any given day, Joel might work on three or four different projects and conduct research on new projects. Since foam behaves differently from metal and has unique tolerances, Joel often has to adapt metal-centric research to suit foam fabrication.
Outside of work, Joel continues to fuel his technical passion and creativity in unique ways. As a musician, he has had a deep love for electronic dance music since the age of 14. This passion for music has allowed Joel to develop a strong understanding of sound design and digital production tools, which ties back to his technical expertise. Whether it’s experimenting with different software, synthesizing new sounds, or creating music, Joel’s commitment to innovation and technical mastery transcends the office, and he brings that same drive for excellence to every project at Kewell Converters. His ability to think creatively and approach challenges with a fresh perspective has made him a standout member of the team, and his outside interests continue to inspire new ideas and approaches to foam fabrication.
Joel’s commitment to sustainability in foam fabrication
Despite working in the foam and plastics industry, Joel remains deeply environmentally conscious and mindful of the impact of his work. “I am environmentally conscious. I know plastics and foam are the best raw material options for many of the long-lasting products we help to fabricate. There simply are not other suitable options available at the moment,” he explains. Joel is dedicated to finding ways to make the production process more efficient and sustainable, ensuring that the materials used serve their purpose while minimising waste. His commitment to sustainability drives him to continually explore eco-friendly alternatives and improvements, all while maintaining the high standards of quality and innovation that Kewell Converters is known for.
Joel’s passion for learning and innovation is helping Kewell Converters stay ahead in the foam engineering industry. By combining traditional techniques with new technologies, he is playing a key role in refining the way foam parts and foam shapes are created. His work in programming, and R&D is not just improving efficiency—it’s paving the way for the future of foam fabrication.
If you need expert advice on foam parts or foam conversion solutions, our team is here to help. Get in touch with us today to discuss your project. Also, be sure to check out our other blogs on Chloe, Micky, and Scot to learn more about the incredible talent driving Kewell Converters forward!