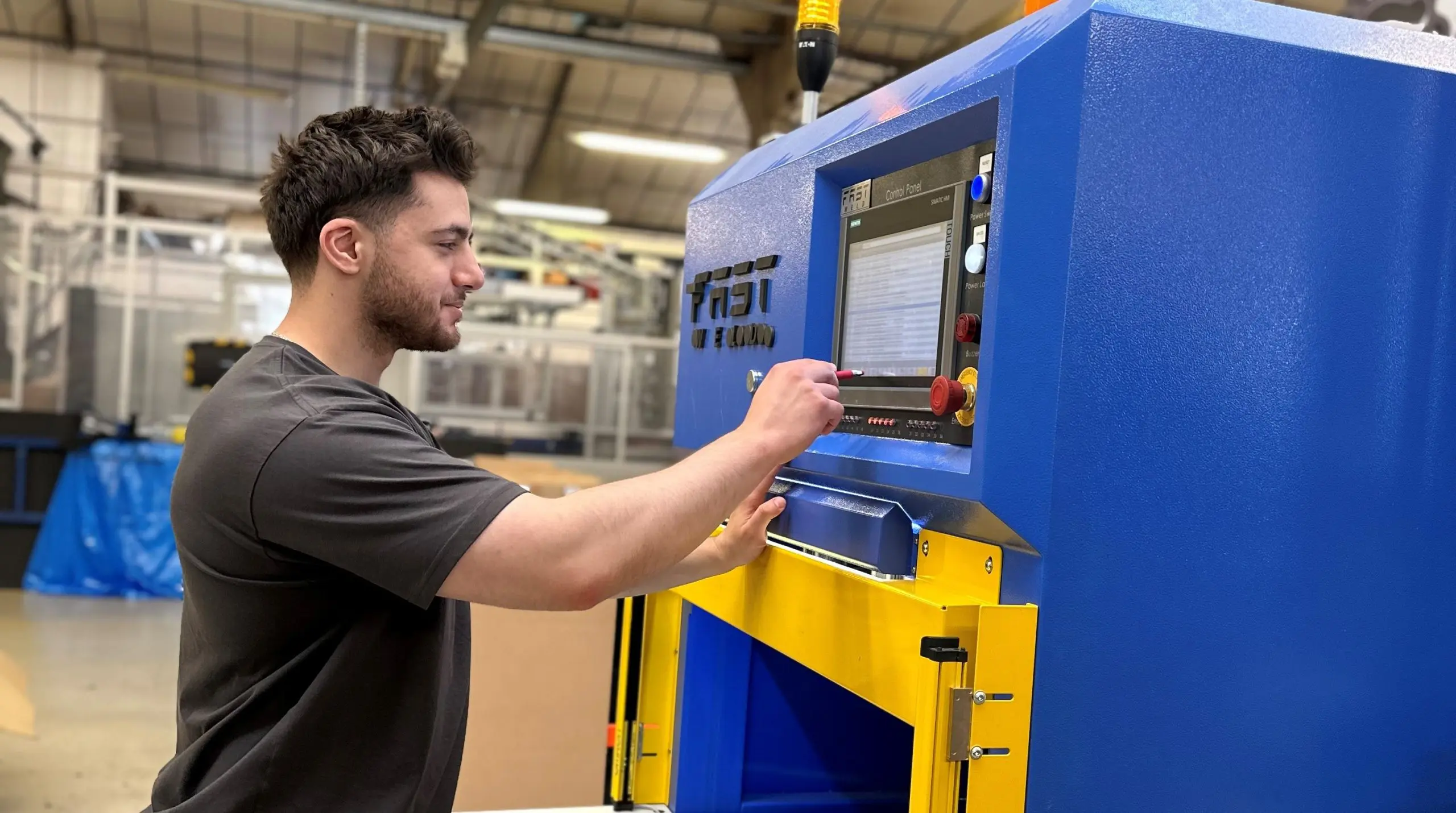
12th June 2025
Production Operator, CNC Team
Read more >
Waterjet cutting equipment is well-known for its prowess in cutting rigid materials, but it has yet to become an equipment staple when cutting soft materials. In fact, there are many advantages of using water-only waterjets to cut materials like foam, rubber, insulation and paper versus the traditional cutting methods of shearing, die cutting or hot wire cutting. Kewell Converters Ltd (KCL) owns 3 water-only waterjet machines—all with two (dual) heads per machine at their modern production facility under 1 roof along side x3 Multi head CNC Routing machines and many other foam converting/fabricating machines.
As water-only waterjet cutting becomes more popular among foam and rubber converters, many companies wonder what allows their competitors to have the advantage by using a waterjet system. Here are the most notable water-only waterjet advantages:-
When cutting with water-only, the stream of high pressure water is very narrow which results in a very small kerf. As a result, multiple shapes on a sheet can be cut with shared edges to save production time and material.
Water-only waterjets are designed using lighter, faster drive systems.
It allows operators the ability to stack material prior to waterjet cutting. There is less of a difference in cut from top to bottom with a waterjet because there is no compression of material like there is in other methods like die cutting.
Water-only waterjet cutting allows operators to prototype a part easily and quickly. In a matter of minutes, you can go from a drawing to a CNC file to cut a part without expensive dies or complex methods. This allows for changes to an existing cutting process without paying for expensive dies or machine changes.
Many traditional methods of cutting harder durometer materials all the way to spongy, soft materials are only capable of simple cuts. For complex shapes, dies are often purchased but they are expensive and not easily modified. Water-only waterjets are a versatile cutting solution that does not require any added tooling costs to produce parts.
One of the most important advantages of waterjet cutting is that there is no heat affected zone (HAZ) commonly found in hot wire cutting. Additionally, there are waterjet cutting methods that will minimise the wetting of materials while it is being cut.